Genesis
of new aircraft types
"Everything
there ever was, was once just a dream"
Part
I - Velocity
Part
II Atlantica
Taking a
new concept to reality requires vision, know how, money and hard work. If
we never acted on our dreams human kind would not even have fire and the
club. Fortunately we do act and our standard of living gets better as a
result. Development of new aircraft is part of this process.
Velocity Genesis
The
Velocity was conceived and acted on by Dan Maher in Dec of 84' as an
improvement to the popular Rutan design, the EZ. He had seen the molds and
assembly I was finishing up on another prototype called the "Sea
Shark". Dan liked my craftsmanship and invited me to work for him on
his new project so I started in the first of Jan 1985. He had begun the
fuselage and showed me the planform - it was sketched on a
napkin
As
we constructed components, detailed design decisions were made as we went.
Soon word leaked out that we were building a 4-place EZ type that aroused
many naysayers as well as constructive help. Ted Yon, EAA since 1954,
senior aerospace engineer, played the most important role advising on
rigging and structures. Ted, who is now also a FAA designated engineer,
did the span loading and resulting spar cap lay-up calculations as well as
our Wiffle Tree design.
The
scratch-built prototype flew in August of the same year. This pretty
little #1 Velocity exceeded all our expectations. The aerodynamic
engineering had been very basic but experience, intuition, luck and
stubbornness paid off.
I then
built the kit molds and started up production. While away from the
factory, I built my own personal Velocity that served faithfully for
years. With my own aircraft and bush pilot past I was able to push the
low-speed end of the envelope marveling at the Velocity's stable,
stall-proof characteristics. The Velocity was the first modern kit that
had utility, style, speed but most important of all it was relatively easy
to build. The reason for this was that Dan and I used our prior boat
building experience to modularize the components. This integration of many
parts into just a few big ones produced the industries first true
"fast built" kit.
This was
done by design such that less assembly was required as the parts came from
the mold not because of factory post molding sub-assemblies. As the
Velocity became more popular the need for a better method of wing
fabrication became obvious so I formed Dynamic Wing Company and started
the evolution of my new solid core pressure molding.
Like the
Velocity itself, the closed molding system my team and I perfected worked
better than anticipated. We have since delivered over 180 complete sets of
wings to very happy customers.
Part II
ATLANTICA
This is the
culmination of over 30 years of aerodynamic and composite study and
experimentation on my part. My curiosity in these areas started at a young
age. In 1962 when I was 12, I built a gas powered flying wing of my own
design that provided many hours of fun. That same summer I built my first
surfboard that was also a lot of fun until a big wave broke it in half.
This was just the beginning of my lessons in structural engineering. At 8
years of age I won the first sail boat race I entered. At 16 I won the
first surfing contest I entered and at 18 I supervised the hull design and
lay-up, helping my older brother win the Bahamas 500 off-shore powerboat
race. In the late 60's I started using epoxies and multiple fins on my
surfboard designs. I had a garage at the time and went through a period of
rapid development in board shaping. I have since seen many of my ideas
become the standard. While in ocean engineering school, I developed my own
hydrofoil design that was later adapted to carbon fiber wind surfers I had
made. This challenging development in fluid dynamics and structures I've
always done as a competitive hobby with no commercial intent.
My full-scale aircraft
experience didn't come about until I was in my twenties. I had a P-18 and
later bought the first 540 Lycoming Powered Maule and flew it down to
Costa Rica to run our ranch. I used that plane as a real workhorse and
gained an understanding of low speed flight and stall characteristics.
When I returned in '79 I went to Oshkosh, camped out of my Maule, and had
my eyes opened up to an entire world of possibilities where I could use my
design and composite skills to do something that I love.
The Atlantica is a
relatively recent development for me with it's roots starting at Sun N'
Fun '97. I had my pressure molded wings on display with some models of my
slide-rule designed aircraft in front. A fellow stopped by to talk design.
He turned out to be a top-level military aerodynamic engineer from Wright
Pat. He was unable to give up "secrets" but showed interest in
my highly integrated wing molding process. Later on, he dropped by a
second time and pointed out that my process lent itself to easy
construction of some emerging designs.
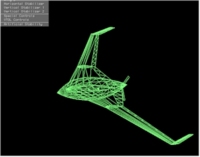
In 1998, I met Austin
Meyer, a young aeronautical and computer whiz who had developed an
intriguing software package using Open GL in order to provide extremely
realistic simulations. The
program, X-plane
is based on blade element
analysis and calculates moments to a high resolution in real time (at
least 15 times per second). The graphics interface of X-Plane makes it
appear to most people as a simple flight simulator game but it is based on
real engineering and I immediately saw its potential as a concept design
tool.
Over the next year I
designed hundreds of airplanes with this tool, and worked closely with
Austin verifying the program's accuracy. This was FAR more advanced
than the napkin sketch that started the Velocity (see part I)
What
evolved resembled a bird by the time performance and handling had been
optimized. This fairly conventional design had great numbers and style,
but as I studied closely how to produce my "x-bird" its
complexity of manufacture and high parts count became glaringly evident.
In Dec '98 I remembered that nice man from Wright Patterson and the BWB
that had "pitch
generating capability". I knew it would be easy to build, especially
with my proprietary Pressure Molding Process, but how would I make it fly
right? This sent me off researching for what BWB's really looked like.
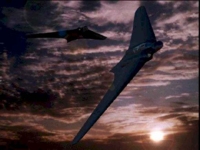
By 1944 the Horten brothers' flying wing HO-9 had advanced into a partial
BWB with some very important rigging and control features. Critical
details that are essential to stability.
The next place I went
was NASA, which led me to Dr. Ilan Kroo's work at Stanford University.
Then I took a closer look at the many renditions of future military
designs discussed in "Aviation Week" and other resources.
With a refreshed
understanding of the BWB as compared with Flying Wing designs, I returned
to a component of X-Plane, called "Plane-Maker . This
allows the user to create an aerodynamic model of anything imaginable
(pretty much) and fly it in the real-time simulation of X-Plane. The
results of entering a BWB configuration were immediate and dramatic.
By the time Sun N'Fun came
around, I had several models of personal BWB's that out-flew any of my
previous designs.
Then with my notebook PC
and X-Plane, I was able to show these designs - in flight - to many old
friends. It was very exciting but their reactions were skeptical. I found
myself reminding them that the math hadn't changed. "X-Plane replaces
all of the pencil pushing that 'slide-rule' designers labored over for
months in order to understand a new shape, only in real-time."
At this point I had over
a year's experience with the program and a good rapport with it's author
developed over long conversations regarding the accuracy of the program.
The "control" aircraft that came with the program, like the 172,
Baron etc. all fly correctly as personal experience has shown me. The
program and blade element analysis provide very realistic output,
including failure modes, and gusty weather situations. Likewise, my own
designs always reacted to changes in a logical manner.
It is more accurate than
scale models, and has advanced the design process beyond any point that I
expected to experience or had available when I helped build the first
Velocity.
Later
in '99 I started using Dr.
Hanley's "Visual Foil" software to find the correct airfoils
to further optimize my Personal BWB designs. First I analyzed the Reynolds
numbers for sections across the span. Then I used this information in
conjunction with my specific rigging requirements to search for the proper
airfoils for each station on the Z-axis. In the software's library of over
one thousand airfoils I was not able to find any that provided docile
characteristics, laminar flow and allowance for efficient rigging at the
same time. As a result I had to design my own new family of airfoils to do
the trick.
Fortunately,
computer wind tunnels are more accurate and less likely to lead a designer
astray because testing is always done with full-scale Reynolds numbers.
This is important because most wind tunnels are operating with air that is
at sea level pressure density. Air molecules affect aerodynamics in
proportion to the size of the body being acted on as well, so a small
model in a real wind tunnel is effectively flying in pea soup, hardly as
accurate as we like. (Here is a strange case of the virtual model being
closer to reality than a physical model)
Once the airfoils were
complete, I went back to my old fashioned drawing board with a pencil and
worked out the internal details. This includes ergonomics, mechanics and
structures. The BWB shape really lends itself to the plumbing and hardware
space requirements of an aircraft. The cabin is free of a center tunnel,
and still has 10cu ft. of cargo with room for skis or a long surfboard.
Finally I was able to
plot some full sized templates for the mold masters. The
technique I use to make these forms is just a jumbo version of what a
professional surfboard shaper taught me in 1966. I take foam blocks, cut
them, and shape bevels before rounding. The
system is very accurate and fast for someone like myself who has shaped
hundreds of surfboards.
It helps also in this
case that the designer, draftsman and toolmaker are all in the same head
... mine